Vinyl Ester Resin Bund Lining Systems
Vinyl Ester Resins
Vinyl Ester Resin, or Vinylester as it was originally called, is a synthetic resin produced by the ‘esterification’ of an epoxy resin with an unsaturated monocarboxylic acid. ‘Esterification’ is basically the chemical term for a process involving the interaction of a compound possessing a hydroxyl group with an acid, and the elimination of water. The reaction product when the base compound used is an epoxide material is known as a ‘Vinyl Ester’, which is a solid that is then dissolved in a reactive solvent, usually styrene and by around 35 – 45% by weight.
There are also some compounds that are marketed by chemical companies as ‘Epoxy Vinyl Ester Resins’ and/or ‘Novolac Epoxy Vinyl Ester Resins’ – although these particular formulations / grades of vinyl ester resin are not for site use as they are extremely sensitive in mixing and application, so can only be used in strictly controlled factory envionments.
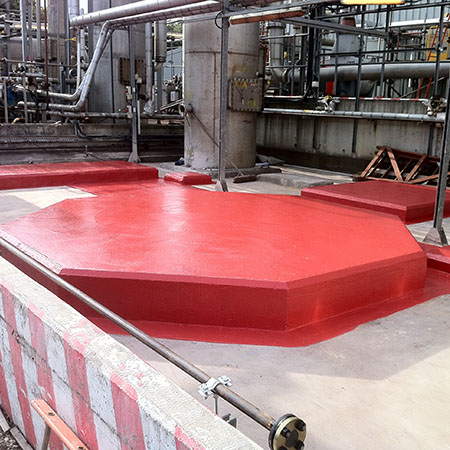
Vinyl Ester Resin Bund Linings
The vinyl ester resins that are suitable for use in formulating bund linings and protective coating products can be used as an alternative to polyester and epoxy materials in as the matrix or in composite materials, where they have the performance characteristics of strength, chemical resistance and cost between those of polyesters and epoxies. However, vinyl ester resins generally have a lower viscosity (approx 200 cps), than polyester (approx 500cps) and epoxy (approx 900cps), which means that products produced with them can be extremely free-flowing and easy to apply, such as in the build up of laminated Fibre / Fabric Reinforced Plastic (FRP) bund lining systems.
This applies to both factory produced prefabricated bund liners that as mentioned previously are ideal and cost effective for smaller self contained bunds, and they can also be used for larger on-site laminated system build-ups, in mortar matrices and as protective coatings, where the vinyl ester resin based product has the necessary chemical (they are particularly good for acid rsistance), mechanical resistance and other suitable – plus theyare fast curing and hardening in cmparison with most epoxies is also an advantage. However this combination of fast to very fast curing and hardening with a relatively high solvent content, means that vinyl ester resin materials cannot and should not generally be stored or used at higher temperatures for the obvious health and safety / fire risk reasons.
There is also now a so called ‘new generation’ of styrene-free vinyl ester resins or epoxy vinyl resin products that have started to be promoted, but this is mostly marketing speak and these materials should correctly be called Epoxy Acrylate Resins, as although their production and process is similar to that of the the Epoxy Vinyl Ester Resins, the modifier in the production process is a dimethacrylate, and the styrene solvent is replaced because the dimethacrylate is also used as the reactive solvent – As a result of this similarity some grades of these Epoxy Acylate ‘Vinyl Esters’ are claimed to be solvent free. However as stated this would seem to be for marketing purposes to take advantage of the well establishe corrosion resistance of Vinyl Ester Resins, as technically these products are really ‘Epoxy Acrylate Resins’ and have significantly inferior properties – NCC Bund Lining experts do not recommend them and consider they are being unwisely over-sold.
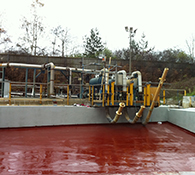
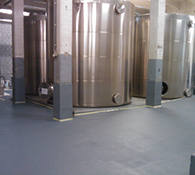
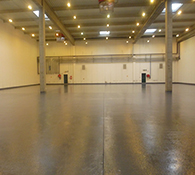
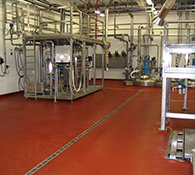
So to summarise the advantages, disadvantages and limitations of real vinyl ester resins:
Vinyl Ester Resin Bund Lining Advantages
- Good resistance to acids and alkalis, including strong nitric acid
- Good resistance to hydrocarbon solvents
- Excellent resistance to strong oxidising agents i.e. chlorine bleach
- Fast to very fast curing and hardening
- Lower cost than pure epoxy resins for FRP component manufacture
Vinyl Ester Resin Bund Lining Disadvantages
- Solvent containing materials
- Difficult to apply at lower temperatures
- Cannot be stored or used at higher temperatures
Typical Uses of Vinyl Ester Resin Bund Linings
Vinyl ester resin products are used most extensively today to manufacture FRP tanks and vessels as per BS4994: "Specification for the design and construction of vessels and storage tanks in reinforced plastics", in the off-site prefabrication of vessels and components, which are widely used in industrial equipment and structures such as for chemical storage tanks, pipes, process vessels, hoods, ducts and exhaust flues.
The air handling / cleaning and water treatment sectors are also now increasingly using vinyl ester-based composites to replace metals and achieve unique and light weight structures that also withstand corrosive attack. Vinyl ester resins also have a long history of this type of application, for example they are used to fabricate components for use in the Power Industry, particularly in Flue Gas DeSulphurisation (FGD) processes as a cost-efficient and reliable alternative to metals to withstand the highly corrosive environment of the FGD process.
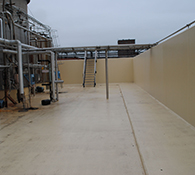
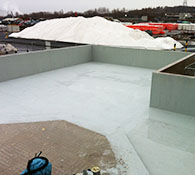
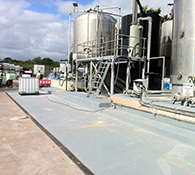
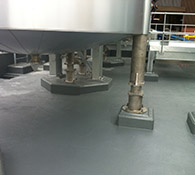
They are also widely used in the marine and boat building industry due to its overall corrosion resistance and ability to withstand water absorption.
There are also a lot of useful motars produced with vinyl ester resins that are mixed to incorporate silicate and other acid / chemically resistant fillers and aggregates, including specialist products for chemically resistant screeds and brick / tile bedding and jointing materials. This type of vinyl ester resin combination is also used multi-layer Glass Flake system build-ups, which are widely use in industrial process areas with high concentrations of acid and strong oxidising agent requirements, such as those that are necessary in galvanising plants, acid production facilities and again in the Power Industry – they are particularly useful for the lower temperature condensate areas of FGDS systems to protect steel and concrete structures.
The specialists at NCC Bund Lining can advise you on the most suitable vinyl ester or other resin bund lining or protective coating solution and appropriately experienced specialist contractors for your specific project needs. Please call any of our offices for assistance from our coating and lining experts.