Bund Lining Systems - Alternative Bund Lining Build-ups
There are basically three main alternative ways of building-up a resin lining or protective coating system in bunds and containment areas on site. This is firstly dependent on the types of resin systems / products selected and then the best system build-up method for each project is determined by a number of other factors including: the substrate profile after surface preparation has been completed – i.e. what pre-treatment and priming is required; the total resin system thickness required for the defined performance; the specific resin products selected - including their consistency, pot-life, application method / characteristics and any environmental or other limitations, including the possibility for the release and escape of any solvent or water contained in any of the system components, plus the products tolerance and sensitivity to the environmental conditions itself – normally moisture and / or temperature sensitivity must be considered.
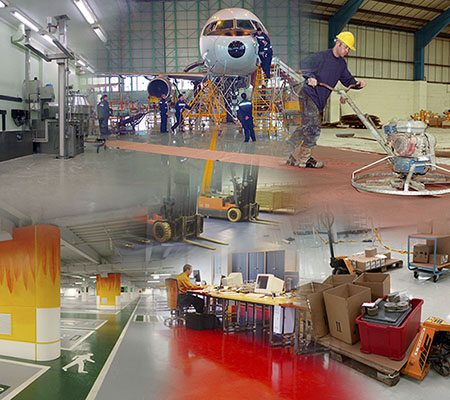
The alternative bund lining system build-ups that are most commonly used are:
- Multi-Coat Rolled or Sprayed Bund Lining System Build-ups
- Self-Smoothing Bund Lining System Build-ups
- Trowel Applied Bund Lining - Screeded System Build-ups
These methods and the difference between these different build-ups of resin bund linings and protective coating systems for containment area can be summarized as follows:
Multi-Coat Rolled or Sprayed Bund Lining Systems
The resin bund lining system is built up from a number of layers of the same or compatible resin products that are generally brush, roller or spray applied, as thick-layer or ‘high build’ coatings, that are thereby ‘built up’ and create the defined system thickness and structure required.
Spray application is obviously the fastest method for larger areas, but brush or roller application may be more suitable for porous and textured or roughened surfaces – This is done to ensure that there is no surface pinholing or voids in the material, which is particularly important with the first or priming layer of the system that is critical for adhesion to the substrate. Multi-coat resin build-up systems are the most commonly used bund lining solution today and they are normally used for Bund Linings and protective containment area coating systems with a total defined thickness from around 500 to 1000 microns or sometimes more (0.5 to 1.0 mm) The broadcasting of suitable aggregates into the freshly applied resin material can also be included on horizontal and slightly sloping surfaces, nin order to provide additional slip or skid resistance, which can obviously be important for areas that will also be exposed to pedestrian or vehicular traffic for access where required. Although increased profile for slip and skid resistance can make cleaning more difficult in any areas with frequent spillages, so this must also be considered and possibly slip resistant profiles can be created just in the necessary walkways or traffic routes for example.
Reinforcing materials such as special fabrics can also be embedded into the freshly applied resin coatings. These include various forms of glass, aramid and carbon fibre reinforcing fabrics that can be selected according to the exposure and performance requirements of the specific lining or containment project. Different types of lining system reinforcing fabrics can be used for many different reasons in multi-coat bund lining system build-ups. THis is because different types and grades of reinforcing fabric produced with different types (polyester, glass, aramid, carbon etc.) and different configurations (woven and non-woven, uni-directional and multi-directional etc) of fibres can be designed to: increase the load bearing capacity and strength of the structure itself; to add increased resistance to the system against impact, abrasion or blast forces; increasing lateral cohesion and reducing the possibility of any future movement; reducing or preventing cracking in the structure or substrate being reflected and going through the system, to ensure watertightness and prevent leakage or contamination for example.
As previously mentioned, these Multi-Coat System Build-ups are now the most commonly used methods of providing durable bund linings and protective coating systems for containment areas, which is due to their almost unlimited possibilities in terms of their design, structure and performance in service. With the right preparation and resin system selection they can also be installed in almost any environmental conditions, plus other advantages or functions can be incorporated such as structural strengthening and upgrading of capacity or load bearing capabilities.
Self-Smoothing Bund Lining Systems
Resin products that are trowel or squeegee blade applied for chemically resistant industrial flooring systems for example, can also provide useful bund lining systems; obviously this has to be on predominantly horizontal and slightly sloping areas, where their application and performance characteristics are suitable. However, as the walls, upstands and any other vertical surfaces in the bund or containment area, are not normally trafficked or so severely exposed to attack, thinner layers of the same or modified grades of these resin materials can be used. These are then applied on these vertical or sloping surfaces by brush, roller or spray.
Self-smoothing epoxy, vinyl ester, PU and polyurea resin systems are all usually applied in 1 to 3 layers to build up the required thickness of these systems, including the application of resin primers where required to seal porous substrates and prevent air or moisture blistering in the subsequent top coating layer. The intermediate or top coating materials are then applied at thicknesses of from 2-6 mm in total, according to the specified lining system requirements. The freshly applied resin layer is then rolled in two diametrically opposed directions with a ‘spiked-roller’ whilst it is still ‘wet’, to remove any entrained air from the mixing and application operations; plus encourage the flow or self-smoothing of the material before it cures and hardens. This surface can then either be left smooth as an easy to clean finish, or alternatively, whilst still ‘tacky’, it can be broadcast with fine graded sand or other synthetic aggregates, with or without an additional sealer coat of the resin, to provide an increased level of slip or skid resistance.
Trowel Applied Bund Lining - Screeded Systems
These are the type of bund lining systems that are used to provide the highest levels of mechanical impact, abrasion and thermal shock resistance. This type of resin system is produced with trowel applied resin mortar systems that are usually based on solvent free resins to prevent any voids or entrapment. The resin is highly filled with selected and graded special sands, or other specially prepared hard aggregates, in order to provide the high impact, wear and shock resistance demanded. These are obviously easier to use and install on predominantly horizontal or only slightly sloping surfaces and limited areas of any associated upstands – where the full mechanical abrasion and wear resistance is less likely to be necessary and thinner coating layers of the resin material alone can be used to provide the chemical resistance and any other specified performance and properties.
Therefore these trowel applied resin screed system build-ups for bund linings are normally laid with traditional‘floor-screeding’ techniques, including machine mortar screeding and power-float finishing techniques. The thickness of trowel appliedresin systems is normally recommended and specified to be from an absolute minimum of 4mm, and more frequently from at least 6 to 9mm in total. This is in order to get the maximum advantages and benefits from this type of protective resin surfacing system i.e. the increased mechanical impact, wear and thermal shock resistance etc. These trowelled mortar bund lining systems can be laid so that they are impermeable in themselves, which is why they are widely used for hygienic, easily cleaned, chemical and abrasion resistant floor finishes in the food and beverage industries for example. However, there may also be an additional requirement for afinal resin sealer coat of the same pigmented resin binder, or possibly another resin based sealing coating, where absolute impermeability and the highest chemical resistance is required – this coating will be brush, roller or spray applied dependent on the material selected for this purpose.
Selecting Your Bund Lining System and the Optimum System Build-up
If you would like any additional help and assistance in selecting the right type of resin system and the appropriate ‘build-up’ for your project,with specific advice and guidance on any aspect of your Bund Lining– no matter what size the area, or your performance demands, then please call any of our offices and one of our specialists will be pleased to assist you.