Bund Lining & Containment in the Oil, Gas & Petrochemical Industries
These industries are grouped together because of their similarities, although there are also considerable differences which we look at later. One of the main similarities is that they are all covered by increasingly strict and actively enforced standards and regulations from the EU and internationally, to tightly restrict and control emissions, pollution and contamination of the environment. As a result reliable and effective bunds and containment areas are required throughout the different facilities involved, plus these must be adequately waterproofed and resistant to the specific chemicals used or stored in each location.
NCC work with many different companies in all of the ‘Downstream’ areas of these industries. This includes from the crude oil or gas being received on-shore, throughout its handling, processing and formulation into countless products and distribution for numerous applications, to their distribution, sale and storage as finished products at domestic and commercial premises, including all of those areas used for the collection, storage, treatment and recycling of oil and other waste materials.
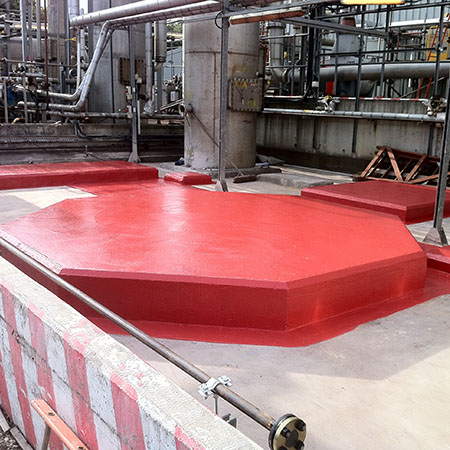
Additionally we have our network of Specialist Contractors that are actively involved with bund lining and protective coating and sealing applications for containment areas every single day. Therefore the service available from NCC includes FREE independent advice on the best bund lining or protective coating solution for your project, plus where you do not have your own experienced Facilities Management Team that we can train and support to do the works efficiently, then we can recommend experienced Specialist Contractors who can give you a complete and professional installation. Another advantage of NCC is that in addition to our expertise in lining and protective coating technologies, our specialists are also experts in the repair of concrete and masonry structures, joint sealing and waterproofing solutions. – A complete advisory and materials supply service.
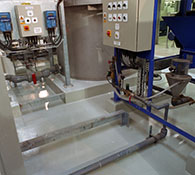
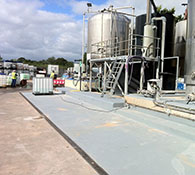
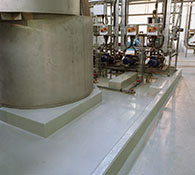
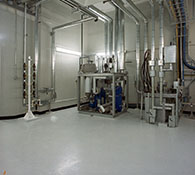
Some additional Background on these industries and the type of areas we are working in are outlined below:
The Oil Industry
The oil industry is broadly speaking composed of three main segments, the exploration and production of crude oil that is shipped to the onshore refineries, then the refining of crude oil into finished products, plus the distribution and sale of those products to end users.
Bund Lining for the Oil Industry
When the crude oil is brought onshore, it is first unloaded and stored in a crude oil tank farm, and then it is treated to remove water, grit and any other minerals, then the different refining processes can begin. An oil refinery consists of a wide variety of processing units in each facility, some use physical separation processes whereas others are based on chemical processes. All of these different process locations have zones and specific plant that require secondary containment in bunded areas, with suitable protection of these bunds and containment structures against the specific chemicals involved in each of them. NCC specialists can advise on the most suitable solution for all of these different containment and bunded areas, on both new build structures and in refurbishment – An important difference in refurbishment projects being the additional damage, contamination and damp conditions that will normally exist. NCC is your ideal partner for these projects due to our additional expertise in concrete repair, waterproofing and the use of moisture tolerant protection systems for bund lining.
There are huge range of different refining processes and also of refinery configuration and layout. There are also additional service and functional processes and structures that are essential to support the actual oil refining operations, including boiler houses for heating and steam generation, cooling water intakes and storage tanks, together with their own waste water collection and storage tanks, plus possibly their own power generation plant. There will also be specialised emission control equipment such as sulphur recovery units or flu gas desulphurisation plant (FGDS) for example. All of these require secondary containment and the containment structures need suitable protection against the relevant aggressive chemical exposure, which NCC can assist you in achieving successfully.
To understand some of these requirements the following is a short summary of some of the typical oil refining processes and the chemicals and activities involved:
Crude Oil Separation Processes
Crude oil consists of a mixture of hydrocarbon compounds including paraffinic, naphthenic and aromatic hydrocarbons with a small amount of impurities such as sulphur, nitrogen, oxygen and metals. The crude oil separation processes ‘separate’ these different components into common boiling-point fractions: liquefied petroleum gas (LPG), naphtha, atmospheric middle distillates, vacuum distillates and residual heavy fuel oils.
n other words, in the first phase of refining operations crude oil is separated into its major compounds using three physical separation or distillation processes according to the temperatures at which they boil or vapourise i.e. atmospheric distillation, vacuum distillation and light-end recovery (gas process).
Bund Lining for Crude Oil Cracking and Conversion Processes
There are three different types of conversion process used in oil refineries:
- Crude Oil Cracking processes are used to break large petroleum molecules into smaller ones. These processes convert the heavier oil products – for which there is generally a lower value and demand – into lighter products, such as diesel and petrol. Dependent on the composition of the crude oil entering the units, the resultant product streams can contain large quantities of petrol and other valuable middle distillates such as diesel and kerosene.
- Alkylation processes are used to combine small molecules into larger ones that are then suitable components for petrol or diesel blending.
- Isomerisation and Reforming processes are used to rearrange the structure of petroleum molecules to produce higher-value molecules of a similar size. These new molecules could have a higher octane number than the original ones and are therefore a more valuable petrol blending component.
Bund Lining for Additional Oil Refinery Processes and Product Handling
Treating processes are then used to stabilise and upgrade petroleum products by separating them from less desirable products and removing any undesirable elements such as sulphur with processes such as hydrodesulphurisation, chemical sweetening, and acidic gas removal.
Additionally further processes can include asphalt blowing for polymerising and stabilising asphalt to improve its weathering resistance, which is important for its applications in roads and roofing.
Finally, the refinery ‘end products’ or ‘finished goods’ have to be stored in bulk or packaged, then loaded for dispatch to customers and the Distribution and Sales segment of the oil industry.
All of these refining processes and specialised equipment need secondary containment and the containment structures themselves need suitable protection against the relevant aggressive chemical exposure, which NCC can assist you in achieving successfully, please call any of our offices and one of our experts will be pleased to assist you.
Bund Lining for Auxiliary Refinery Equipment and Facilities
Every refinery will use additional units and processes which are not directly involved in the refining of crude oil, but are vital to the operation of a refinery. Examples of these are steam boilers, waste water treatment facilities, hydrogen plants, cooling towers and sulphur recovery units.
The size of auxiliary facilities themselves can also be substantial e.g. for the supply or generation of clean water, steam, electricity and process heat, which are required to some extent by most of the individual process units throughout the refinery.
All of these also need secondary containment and the containment structures themselves need suitable protection against the relevant aggressive chemical exposure, which NCC can assist you in achieving successfully.
Oil Refinery Products Most crude oil refineries therefore produce a wide range of products and typically these include:
- Gases such as LPG (liquefied petroleum gas) which can be used as feedstock for chemical processes, as fuel for heating and cooking or as transportation fuel.
- Naphtha, which is mostly used as chemical feedstock
- Gasoline, for transport fuels
- Kerosene, predominantly used as aircraft fuel
- Middle distillates consisting of: diesel fuel, heating oil, Heavy Fuel Oil (for power stations and industrial boilers), Bunker Fuels (for shipping)
- Speciality products including: Lubricants and greases (automotive & industrial), Bitumen (mainly for roads and roofing) and hydrocarbon solvents.
All of these products require primary and secondary containment in storage and handling so once again NCC are the ideal partner to help you ensure that tyour investment in the tanks and containment structures in your facility are also adequately protected with durable protective coatings and bund linings. In addition of course to helping you minimize any risk of pollution and contamination of the environment.
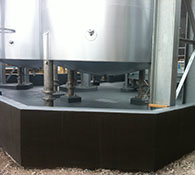
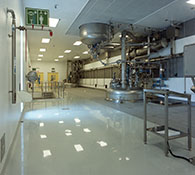
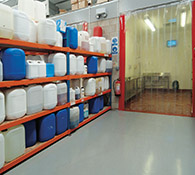
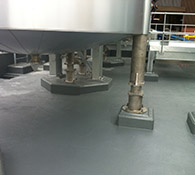
The Gas Industry
The gas producers deliver gas to the 9 UK terminals from offshore facilities at fields beneath the sea around the British Isles and through pipelines which connect to the UK from Norway, Holland and Belgium. In addition, recently commissioned terminals at the Isle of Grain and Milford Haven allow liquefied natural gas (LNG) at extremely low temperatures, to be delivered to the terminal by ship all over the world.
The natural gas used by consumers is composed almost entirely of methane. However, natural gas found at the wellhead, although still composed primarily of methane, is by no means as pure. Raw natural gas comes from three types of wells: oil wells, gas wells, and condensate wells. Natural gas that comes from oil wells is typically termed 'associated gas'. This gas can exist separate from oil in the formation (free gas), or dissolved in the crude oil (dissolved gas). Whatever the source of the natural gas, once separated from crude oil (if present) it commonly exists in mixtures with other hydrocarbons; principally ethane, propane, butane, and pentanes. In addition, raw natural gas contains water vapour, hydrogen sulphide (H2S), carbon dioxide, helium, nitrogen, and other compounds. All of these contaminants have to be removed, down to a certain level in the field and then in a gas refinery onshore.
Bund Lining for the Gas Industry
Natural gas processing consists of separating all of the various hydrocarbons and fluids from the pure natural gas, to produce what is known as 'pipeline quality' dry natural gas. Whilst some of this necessary processing must and can be accomplished at or near the wellhead or source,often at sea on platforms near the UK coast, the complete processing or refining of natural gas takes place at an onshore refinery with sophisticated processing plant.
Processing natural gas is complex, but usually involves initial cleaning or ‘scrubbing’ and four main processes to remove the various impurities including Oil and Condensate Removal, Water Removal, Separation of the different Natural Gas Liquids, Sulphur and Carbon Dioxide Removal.
Obviously all of these different materials need to be handled, stored and loaded or unloaded on or from being transported without pollution of the environment, so these activities must all be carried out in bunded secondary containment areas. The containment structures themselves need suitable protection against the relevant aggressive chemical exposure, which NCC can assist you in achieving successfully, please call any of our offices and one of our experts will be pleased to assist you.
Bund Lining for the Gas Distribution Network
After treatment the gas is transported around Great Britain through over 278,000 kilometres of iron, steel and polyethylene mains pipeline. From the terminals, gas enters the national transmission system (NTS), which is the high-pressure part of National Grid's pipeline network, where it is pushed through the system using 23 strategically placed compressor stations. The NTS supplies gas to UK end consumers from over 175 off-take points including large end users which are primarily large industrial consumers and power stations, who receive gas directly from the national transmission system rather than through a distribution network, and the twelve local distribution zones (LDZ) that contain pipes operating at lower pressure which eventually supply the smaller end consumers, including ourselves as domestic customers – whoever we actually pay for the gas at home.
All of these locations have zones and specific plant that require secondary containment in bunded areas, with suitable protection of these bunds and containment structures. NCC can advise on the most suitable solution for the bunded area, both for new structures and in refurbishment, please contact any of our offices and one of our experts will be delighted to assist you.
Bund Lining for the The Petrochemical industry
The term ‘Petrochemical Industry’ officially relates to all of the ‘Downstream’ processing of crude oil and gas into products that are sold to both end users and for use in the production of other goods and materials. It therefore includes:
- the transportation of crude oil and gas, including pipelines and pumping systems
- liquefied natural gas systems, including the liquefaction and re-gasification plant and machinery
- oil refineries, petrochemical plants and gas processing
For the purpose of this website and like most other people will use this term for only the industries that take their raw materials from those output from the oil and gas refineries, to produce other materials and products i.e. they are known as Petrochemical Plants.
Whatever is being processed in the multitude of different facilities in this field, from pure chemical synthesis, to plastics and even pharmaceutical intermediary materials, all of these locations have zones and specific plant that require secondary containment in bunded areas, with suitable protection of these bunds and containment structures.
Please also refer to the information contained in the Environment Agency Guidance document for Above ground oil storage tanks: PPG 2, August 2011: “Advice on how to store oil safely in above ground oil storage tanks and comply with the law (excludes oil refineries and distribution depots for which there are several other specific PPG’s issued).”
NCC can advise on the most suitable solution for the bunded areas, both for new structures and in refurbishment, please contact any of our offices and one of our experts will be delighted to assist you.