Epoxy Resin Coating & Bund Lining Systems
Epoxy resin coatings and bund lining systems are probably now the best known and most commonly used type of materials used for bund lining and to provide protective coating systems to containment tanks and other bunded containment areas throughout industrial and commercial facilities in the UK. However it must be clearly understood that there are actually many different types of epoxy resins and epoxy resin based protective coatings and linings, with some quite widely different application characteristics and different performance properties. ‘Epoxy resin’ is a very broad generic term that one recent technical author suggested was rather like saying you need a method of transport with an internal combustion engine – the possibilities and variations range from mopeds to aircraft, boats to trains, Smart cars to Big Macks or Ferrari’s – i.e. there are a lot of otions and they vary greatly in terms of their appearance, size, strength, power, speed, fuel consumption, load carrying ability, maintenance requirements and durability etc.
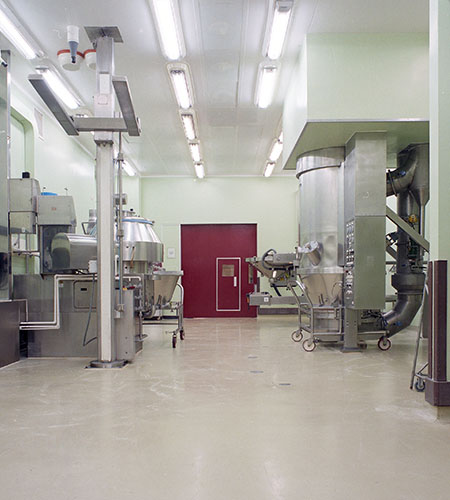
Epoxy Resin Coating & Lining Types
Epoxy resin based products that are used as bund lining materials include:
- Water dispersed epoxy resins (also commonly incorrectly known as ‘water based epoxy resin coatings – they are of course epoxy resin based, and are actually produced from solid epoxy resins that are water dispersible until they are mixed,the epoxy resin reacts and hardens whilst the water evaporates).
- Solvent dispersed epoxy resins – these are similar to the water dispersed products but the water is replaced by a hydrocarbon solvent.
- Solvent free epoxy resins – there is no solvent or water required to disperse these resins , which have a liquid consistence until theyare mixed and react with their hardener to form a solid.
- Phenolic epoxy resins –or ‘Novolac epoxy resins as they are sometimes called after the original material - These are a phenolic compound modified version of the solvent free type and generally these are the type of epoxy resin coating system that have the highest chemical resistance for an 'epoxy' based material.
As always with resin coating technologies, whilst these different types of ‘epoxy resin’ coating and bund lining materials have some similarities in their generic structure, all of these different types of materials also have their own distinct and characteristic advantages, disadvantages, limitations and benefits for their use as protective coatings in containment are as and bund linings. We have tried to summarise the key points of these below and in the following epoxy resin coating and bund lining materials pages to assist you on your projects.
Epoxy Resin Coating & Linings Mixing & Application
The nature and chemistry of epoxy resin products generally makes them the easiest, most reliable and cost effective resin coating materials to mix and apply on site, where they canprovide durable protective coating and lining systems that can last for many years. The mix ratio of a base epoxy resin component to the hardener component, is usually formulated to be around - 4 parts to 1 by volume (4:1), which makes it relatively easy to control the products dosing and ensure thorough and homogenous mixing – This is unlike some other synthetic resins that have much more difficult mix ratios of up to around 20 : 1 and which therefore makes complete and thorough mixing much more difficult and critical, thereby also increasing the potential risk of problems on site.
Epoxy Resin Coating & Linings Advantages & Limitations
Today the UK industry widely accepts that correctly designed and structured epoxy resin based coating and lining systems are a proven, safe and reliable option, for many or possibly almost all but the most critical and onerous installations of primary, secondar containment tanks and bunded areas. The hardness and abraqsion resistance of these epoxy resin coating and lining materials also makes them ideal for use on containment surfaces that will also be trafficked. However, this means that they have to be comparatively rgid and therefore they are not crack-bridging for use in structures where this is an important requirement. Additionally plusbecause of their nature, they are not ideal for installation over existing wet concrete surfaces without appropriate pre-treatment – although this potential difficulty was solved for many situations a few years ago by Sika’s development of EpoCem technology. This technology combines the properties of Epoxy and Cement technologies allowing these products to be applied directly on damp substrates (e.g. whilst the concrete is still ‘green’ or damp in a wet area) and then for the fully impermeable epoxy resin based protective coating or bund lining material to be safely applied the very next day.
Two-component epoxy resin based protective coatings are therefore ideal, and frequently also provide the easiest and most cost-effective solution for the majority of containment and bund lining situations, where the extremely ‘sticky’ nature of the freshly mixed epoxy materials also helps to ensure a good and strong initial and permanent bond to the concrete substrate. The hardened ‘pull-off’ strength of the cured epoxy resin systems is much higher than the cohesive strength of concrete, i.e. meaning the epoxy system can only be removed or damaged through a physical break in the concrete itself. The potential for delamination is therefore minimised and the concrete is reliably protected against impact, wear and abrasion, plus preventing any ingress and attack from water and many other aggressive chemical liquids.
Finally another advantage of good quality epoxy resin based protective containment area coatings and bund linings is obtained through the tight cross-linking nature of the epoxy resin and hardener reaction. This can perhaps be best explained and visualised as being like a physical‘clamping’ effect, which tightly closes the hardened surface, particularly with the solvent-free materials that therefore provide the highest levels of chemical resistance due to this form of almost impenetratable ‘physical barrier’ at their surface. This means that once they have fully hardened or cured, these epoxy resin systems are extremely watertight and will have excellent resistance to immersion and exposure to a wide range of oil and chemical spillages, including aggressive industrial processing liquids and cleaning products – such as strong anionic disinfectants and detergents. Sikagard-62 (also DWI approved) and Sikagard-63 are good examples of reliable solvent-free epoxy resin based coating systems that have been used successfully as bund linings for many years.
The specialists at NCC can advise you on the most suitable epoxy resin product(s) for your specific project needs. Please call any of our offices for specific assistance from our experts.
In the following sub-pages we have also provided more specific information on the particular advantages and disadvantages of each of these different types of epoxy resin based protective coatings and bund lining systems.
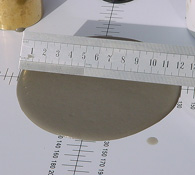
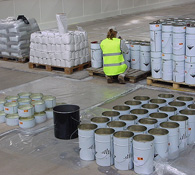
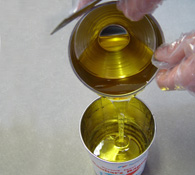
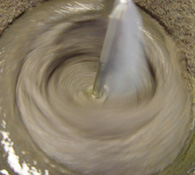
Water Based Epoxy Resin Coatings & Lining Materials / Water Dispersed Epoxy Resin Based Coatings & Lining Materials
Water dispersed epoxy / water based Epoxy Resin Coating materials and systems have historically been considered of limited value in bund lining and protective coatings in secondary containment areas. This was due to their comparatively low chemical and mechanical resistance when compared to other types of epoxy resin materials. However with newer and improved water dispersed resin technology they are now becoming increasingly popular for bunds and containment areas with lower levels of exposure and risk. This is of course due to the advatages they bring in easier and safer application with no solvents or unpleasant odurs, plus the fact that they can be applied on relatively new or damp concrete, plus with the top performing products such as BS 3000 and Sikafloor 2530W, they have significantly increased chemical and abrasion resistance. This is because of the advances in the technology of ‘water dispersed’ epoxy resin based technology, that has been continuously developed and greatly improved by these companies in recent years.
Advantages of Water Based / Water Dispersed Epoxy Resin Coatings & Lining Materials
The main advantages of the water based / water dispersed epoxy resin materials, are that they contain no dangerous solvents, or VOC's (Volatile Organic Compounds) as they are also now referred to, so therefore they can be used safely in occupied areas, and where people and other trades are working immediately adjacent to the area being treated. Plus they can be applied on relatively new or damp concrete surfaces, because they are watertight, yet vapour permeable, and so the hardened coating will not bubble or blister due to entrapped moisture as this can escape over time as water vapour. Additionally these water dispersed materials are not dangerous in the vicinity of naked flames, or sparking from equipment and machinery, or other works in progress. Finally and very importantly for many industries and businesses, there is no odour that can contaminate food stuffs or beverages.
The performance of all water based epoxy coatings against mechanical abrasion and chemical attack, whilst now good for the specific Sika and Remmers products mentioned, it is still and will always be somewhat lower than that provided by good quality and higher build, solvent free epoxy resin products. This is partly due to the normal dry film thicknesses applied being much higher, at more than 300 microns per coat, versus the 100 to 150 microns normally applied with water based epoxy resin products, plus their more tightly cross-linked surfaces formed by the cured resin as there is no water in these products that needs to escape by evaporation in their curing process.
However the multi-coat applications (2-3 coats) of our recommended water dispersed epoxy resin products (i.e. BS 3000 and Sikafloor 2530 W) are very definitely ideal for many domestic, commercial and light industrial, high build resin coating jobs – These applications can include bund linings and protective coatings for secondary containment areas around the primary storage or processing areas for oils, fuels and many other materials.
Water dispersed epoxy resin coating materials also have another distinct and important and possibly surprising advantage over the generally higher performance, solvent-free epoxy materials in relation to their long-term durability and maintenance. This is that whilst it is true that they may be less durable in service, particularly when trafficked, whenever their refurbishment and over-coating is eventually necessary, then the only surface preparation necessary is thorough cleaning to remove any contamination on the existing surface i.e. simply high pressure water jetting and / or detergent cleaning. This is in somewhat stark contrast to the far more complex and sensitive preparation and pre-treatment, including thorough mechanical surface preparation by abrasive keying and frequently also solvent-activation that is necessary to over-coat solvent free epoxy resin coatings i.e. by abrasive blast cleaning or mechanical grinding / sanding followed by vacuuming and then hydrocarbon solvent wiping to remove residual dust and fine particles.
Additionally due to their non-taint odour and no VOC's the water dispersed epoxy resin coatings can be maintained and overcoated indoors and in occupied areas without disruption or danger to others (also true with new coatings and bund lining work) this can be particularly important when there are anyother trades and people working in the same or adjacent areas.
Therefore in many instances the best water based / water dispersed epoxy resin coatings may not have the highest long-term abrasion and chemical resistance , but they may well have considerable other advantages on a specific project. These could be any or a combination of the facts that they are much cheaper, safer and easier to use and that they are available in almost any colour. They will allow easier over-coating with refresher coat whenever they are required -all with the minimum of surface preparation, disruption and cost. This is a very clear example of why the right product / system selection for each bund lining and protective coating project in containment areas, must always be mad with a full evaluation of all of the application and performance requirements for the specific project and its location
Remmers BS 3000 or Sikafloor 2530W water dispersed, epoxy resin based lining, flooring and vertical / wall coating systems are both absolutely ideal to meet the performance requirements for use in many different bunded and containment areas or ground water protection zones in domestic and commercial applications including garages, workshops, light traffic production assembly and storage areas–together with many other light to medium duty applications in the food and beverage industries for example.
If you would like help and assistance with the selection and use of water dispersed / water based epoxy resin systems, then please call any of our offices and one of our specialists will be pleased to assist you. Normally we can also deliver these materials direct to your site, and in the colour of your choice, within 48 hours on the UK Mainland.
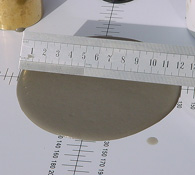
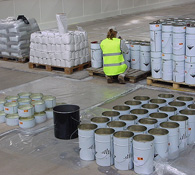
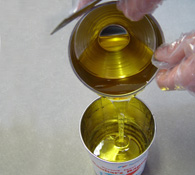
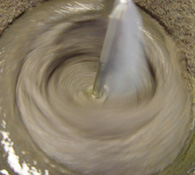
Solvent-Free Epoxy Resin Based Bund Lining Materials
Solvent-free epoxy resin based protective coatings are the most commonly used type of epoxy resins for bund linings and probably also the most commonly used bund lining materials overall. These epoxy products contain no solvents or water as diluents and are therefore said to be 100% solids, although the 2-components are mixed together and applied as a liquid with varying degrees of viscosity and thixotropy. This is because when mixed ready for application, this type of epoxy resin coating product consist solely of the epoxy resin and hardener, plus any other 'fillers' included in the formulation such as pigments and special ingredients, which react and combine to form a high build, dense, vapour-tight, extremely waterproof and chemically resistant solid film with 100% of the same volume of the original two liquid components when mixed together and cured / hardened on the surface.
Solvent-free epoxy resin bund lining products are therefore formulated with a high resin content by definition and generally they can be used in much thicker layers than water dispersed or solvent containing products, where the product thickness is limited because the solvent or water used as the diluent has to escape by evaporation during the curing and hardening reaction time to prevent blistering and bubbling – This is not required with sovent-free epoxy resin systems. As a result these solvent-free epoxy resin lining and coating products also produce a tighter, denser and far less permeable surface to liquids and vapour, which also means that they can have a much higher performance in terms of their chemical resistance, plus the thicker layers mean that they can also provide greater protection against abrasion, wear and mechanical damage in your bunds and containment areas.
Perhaps one disadvantage of these materials is that as a consequence of the much higher epoxy resin content, solvent-free epoxy bund lining products are always going to be more expensive and so they are generally only used by specialist contractors for professionally installed bund lining projects. The UV light resistance is generally good and not a performance issue at the normal higher build thicknesses that these materials are used at (500 – 1000+ microns) but they will yellow over time and surface chalking will occur if exposed to direct sunlight.) Another possible disadvantage on some projects is the time that they require to harden and then achieve their full chemical and mechanical resistance, which is generally up to 7 days at average temperatures of around 20°C - In these situations where far early use and resistance is required, NCC generally recommend the alternative use of rapid hardening polyurea resin based linings such as the excellent range from VIP GmbH.
Solvent-fee epoxy resin coatings are ideal for many bund lining applications and generally these systems are designed for use in areas with medium to the more demanding and higher performance requirements i.e. they are ideal for the lining and protection of primary and secondary containment tanks and bunded containment areas forsewage and waste water treatment tanks, plus many other different industrial and other process and production areas. These systems will also provide excellent resistance to heavy pedestrian and vehicular traffic, due to their high mechanical strengths against abrasion, which is why they are also used extensively for industrial floors in production and process area flooring.
Bund Lining with Solvent-free Epoxy Resin Materials
Due to their high viscosity and thick consistency, solvent free epoxy resin lining products require very thorough ‘compulsory’ mixing with adequately powered mixing equipment prior to their application. The lack of any solvents or other diluents, which would have to be allowed to escape from the material during curing, means that solvent-free epoxy resin materials can be applied and built up in comparatively thick layers. These are normally from 0.3 mm to 2mm per layer, in a sufficient number of layers, typically 2 or 3 layers, to achive the total thickness specified for the desired level of performance. Normally at least two layers of the material are always recommended for linings and protective coatings in containment areas, to ensure that the minimum and nominal specified thickness is maintained over the whole area.
It is also common to use different colours for intermediate layers to give an easy method of visual control. The application of solvent-free epoxy resin linings and coatings can be done by several different methods to suit the specific structure and type of installation including: by brush, roller or spray as high build coatings; flow applied by trowel or squeegee, as self smoothing layers with or without the incorporation of additional fillers or fine sands / aggregates, on horizontal and slightly sloping surfaces, plus these self smoothing layers can be broadcast with graded natural or synthetic aggregates to create even more highly abrasion and wear resistant non-slip or non-skid surfaces within the containment zones.
Priming for Solvent-free Epoxy Resin Bund Lining Materials
For solvent-free epoxy resin coatings and bund linings, additional priming is not generally required, however very porous concrete substrates are usually best sealed or ‘primed’ with clear grades of the same or a similar solvent free epoxy resin product. This is to penetrate and seal the substrate within it’s surface and also eliminate or reduce any suction and ‘drag’ from the surfaces on the lining system during the application, which reduces consumption increases the speed / work rate and improves the appearance of the finish.
This initial sealing and priming also prevents any blistering or bubbling in the finished coating system due to rising air and / or moisture from within the substrate during the coatings curing time. Clear grades of solvent-free epoxy resin primers are also used to obtain increased penetration and adhesion for other types of synthetic resin coatings and bund lining systems as outlined later on this website.
As previously mentioned these solvent-free epoxy resin coatings and bund lining products are usually only recommended for use by professional specialist contractors, however where appropriate for your specific project requirements, NCC can provide guidance, training and support for their use by competent general contractors or your facility maintenance crews i.e. in processing plants and other facilities with high security or restricted access for any other reasons.
NCC also provide specialist advice and specially developed solvent-free epoxy resin coating and bund lining products forvery specific applications and industries, such as systems specially developed for use on concrete surfaces in contact with potable (drinking) water, where the materials must all have DWI Approval in the UK for this specific purpose (such as Sikagard 62N), or for use in the Nuclear Power industry where the materials must all have the highest UKAEA radiation decontamination certificates. Similar products are also now being demanded for other ‘Clean Room’ environments, or with additional defined anti-static or Electrical Static Discharge (ESD) reistance properties for example. Specific advice and these materials are also all available from the specialists at NCC Bund Linings.
If you would like help and assistance with your specific project requirements, please call any of our offices and one of our specialists will be pleased to advise and assist you.
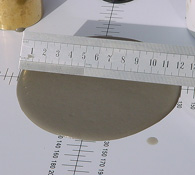
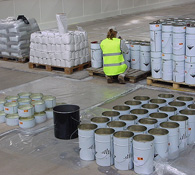
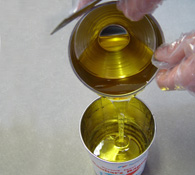
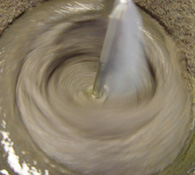
Phenolic Epoxy Resin Based Bund Lining Systems
Phenolic Novolac epoxy resin
Phenolic epoxy resins or Novolac epoxy resins are variations and modifications developed from the technology of the old phenolic resin materials, the first synthetic resins originally developed (i.e. Bakelite) for industrial uses in chemically resistant mortars, coatings and pipe linings in the 1920’s. In phenolic epoxy or novolac epoxy resins the base epoxy resin is modified and hardened with phenol hydroxyl groupings. The chemistry of these materials is now extremely varied, and the information ‘known’ by many people who talk about them has probably got more to do with various American and other companies past marketing hype, than any real organic chemistry knowledge.
The specialists at NCC can advise you on the most suitable phenolic epoxy, novolac epoxy or other resin bund lining or protective coating solution for your specific project needs. Please call any of our offices for specific assistance from our experts.
As Buyer Beware - There is a lot of misinformation passed on and many expensive mistakes in both selecting and in not-selecting one oof these systems on a project. As the way these materials are talked about is so frequently misleading or even completely wrong, we will try and summarise this correctly now – Our apologies that this s somewhat of a technical ‘anoraks’ page and complex if you do not have a Phd in Organic Chemistry (we don’t we are Engineers), but for those who would like the facts here they are as clear as we can summarise as follows:
Phenolic Resins
The first generation of synthetic resin in the 1920’s was of the so-called phenolic resins, which were actually phenol formaldehyde resins (PF), the first such synthetic polymers obtained by the reaction of phenol or substituted phenol with formaldehyde – Bakelite type, mostly produced and set by heating the components (thermosetting resins). The original bulky desk telephones and today these are still mostly used in moulded resin products and applications, now particularly in the platform of printed circuit boards because they are good at being inert and produced in almost any shape, but also for pool and snooker balls or laboratory worktops due to their hard and chemically resistant nature. The main disadvantage for other construction applications is that they are heat cured and due to their hardness, they are also very rigid and not at all flexible.
Novolac Resins
Novolac resins (originally called Novolak) are a further development from the original phenol-formaldehyde (PF) resins, made when the molar ratio of the formaldehyde part to the phenol part is reduced to less than one. An amine hardener then needs to be added to crosslink and cure the material as a ‘Novolac’ resin, in a similar way to the cross-linking (curing and hardening) process of an epoxy resin. These variations are also sometimes called Phenolic Novalac Epoxy resins or various other permutations of these words in the hands of marketing people! Interestingly there are also some of these Novolac resins that themselves can then be used as hardeners for epoxy resins – more on this below.
Resols or Phenolic Resols
Resols are another development made from the original chemistry of phenol-formaldehyde resins by using a different formaldehyde to phenol molar ratio of greater than one (usually around 1.5). The phenol, formaldehyde, water and a catalyst are all mixed and then heated together, where the mix becomes thermosetting and the components react together at around 120 °C to form a highly cross-linked resin that has good hardness, good thermal stability and chemical resistance.
These resols (also known as Resoles and Phenolic Resols) are of considerable importance today that are widely used as hot-melt and hot applied adhesives for gluing and bonding many different building materials during the production and fabrication off-site in factory conditions. This includes plywood, Sterling board or Oriented Strand Boards (OSB), and many other engineered timber products and laminated sheet materials, such as the so-called Engineered Wood Flooring. There are also a few examples of Phenolic Resols being used to produce high early strength and highly acid resistant mortars for special acid resistant brick and tiling applications used in the protective lining of tanks and vessels, but these are not suitable for use on alkaline substrates such as concrete or cement mortar / render.
Phenolic and Novolac Epoxy Resins
Phenolic resins (PF) have also been developed to be used as ‘modifiers’ for various coatings including ‘two component solvent-free epoxy resins. The incorporation of phenolic resin in an epoxy resin bund lining and protective coating product formulation can be used improve the adhesion, moisture sensitivity and increase the corrosion resistance of the coating material.
Some modified phenolic resins (PF) of the Novolac type (molar mix ratio less than 1) can also be used as curing agents or hardeners for a range of different types of epoxy resin based materials. Chemically the phenolic / novolac resins used in these materials are the non-heat reactive materials, which have free phenolic-OH groups in their structure that react with the epoxy groups as a hardener with a very high degree of cross-linking. Since this curing mechanism does not produce any by-products, thick sections may be obtained without voids and stresses and with very low shrinkage, provided the reaction temperature is controlled of course. There are examples of these Novolac or Phenolic Epoxy resins used in many different construction applications including moulding, laminates, adhesives and protective coatings.
Phenolic or Novolac epoxy materials have increased chemical resistance, particularly acid resistance and hydrocarbon solvent resistance. Products with an increased level of this ‘phenolic’ (PF) ingredient, will have the highest levels of chemical and solvent resistance, but if used in a protective coating formulation there is also a consequent loss of flexibility, which must also be considered as a disadvantage. Some phenolic and novolac modified epoxy resin products are also temperature sensitive in their application on site and also they can require significant additional heat curing, which may not be practicable.
Thus – Phenolic and / or Novolac Epoxy resins are basically the same thing, but there is a lot of potential differences between specific resins and the specific products for bund linings and protective coatings that can be formulated with them – So Do Not Take Risks – Check with NCC Bund Lining Experts for the right product and system solution for your bund or secondary containment area lining.
Phenolic Epoxy Resin Based Bund Linings & Coating Systems
The potential Advantages of Phenolic and / or Novolac Epoxy resin based bund linings and protective coatings for containment tanks, vessels and areas include:
- High heat resistance
- Excellent chemical resistance
- Excellent solvent resistance
- Excellent corrosion resistance
- Hard, abrasion resistant film
The potential Disadvantages or Limitations of Phenolic and / or Novolac Epoxy resin based bund linings and protective coatings for containment tanks, vessels and areas include:
- May require heat curing
- Relatively slow air cure
- Non UV stable – will chalks and may discolour
- Relatively brittle
As a result the primary uses of Phenolic and / or Novolac Epoxy resin based bund linings and protective coatings are generally recommended to be restricted to where extreme chemical resistance is required and there is no more practical or cost effective solution available, without the associated disadvantages. In our experience typical examples of the most common applications where it is difficult to replace these products in terms of their performance, with easier to handle and more cost effective solutions, are as steel and concrete tank linings and high risk covered containment areas in refineries and the petro-chemical industries.
The specialists at NCC can advise you on the most suitable phenolic epoxy, novolac epoxy or other alternative resin bund lining or protective coating solution for your specific project needs. Please call any of our offices for specific assistance from our protective coating and lining experts.